The Best Epoxy For Secure Coating
-
Deep Pour Epoxy Resin Kit Crystal Clear Liquid Glass - 2 to 4 Inches Plus Clear Epoxy -
Dr Crafty Epoxy Resin -
TotalBoat Table Top Epoxy Resin -
Loctite 1365736 Heavy Duty Epoxy -
Bob Smith Industries BSI-201 Quik-Cure Epoxy -
J-B Weld 8280 Original Steel Reinforced Epoxy -
System Three 0102K40 General Purpose Epoxy -
Marine-Tex Epoxy Putty -
J-B Weld KwikWood Epoxy Putty -
Permatex 84209 PermaPoxy 4 Minute Multi-Metal Epoxy -
JB Weld 8267 SteelStik Epoxy Putty Stick -
Super Glue Plastic Fusion Epoxy Adhesive #15277 -
Loctite 1363118 Plastic Bonder Epoxy -
Permatex 84145 Permapoxy Black Plastic Welder Epoxy -
Rectorseal 97606 EP-400 Epoxy Putty -
POR- 15 49033 Epoxy Putty -
PC Products PC-11 Two-Part Marine Grade Epoxy -
J-B Weld 8272 Marine Weld Epoxy -
Pro Marine Supplies Table Top Epoxy Resin -
Buyer's Guide
The world of adhesive is vast and sprawling, but the king of the hill has to be epoxy. There is a special kind of epoxy for every application from simple, wooden joinery to plugging leaks in boat hulls. Choose the right one and the end result will be a joint or repair that is both strong and astoundingly long lived.
We've narrowed down our selections to the most commonly-encountered types of epoxy, though this is not meant to be an exhaustive list of every type of epoxy that exists. Our recommendations take into consideration the overall effectiveness of each best epoxy in 2022, value for money, availability both off- and online, user reviews, and personal experiences with each.
The following categories are represented below:
Best All-Purpose Epoxy
Best Wood Epoxy
Best Metal Epoxy
Best Plastic Epoxy
Best Putty Epoxy
Best Waterproof Epoxy
Where applicable, we've included multiple recommendations for your convenience. All of the epoxies selected here are great products, so it ultimately comes down to personal preference.
Here are the best epoxy of 2022
Deep Pour Epoxy Resin Kit Crystal Clear Liquid Glass - 2 to 4 Inches Plus Clear Epoxy - Best Epoxy Overall
Enjoy one of the best epoxies with Upstart Epoxy Resin KIT DIY. In it comes all you need to begin your creative journey, and it is ideal for everyday woodwork enthusiasts and professionals. It has a spreader, two mixing sticks, a video tutorial, and a foam brush. The epoxy materials are made in America, thus guaranteeing only top quality materials which will stand the test of time. This epoxy is made with a transparent and clear finish using its nano-crystal, ultra-glossy technology. The technology boosts the natural beauty of wall surfaces, giving it improved contrast depth, and it gives it a waterproof finish. You can be assured that your surfaces will never fade, yellow, or crack. The epoxy is made of cellular prepolymers, which stand the test of time and retain their unique shine. With its UV stabilizing agents, you will see a reduction in the effect of gloss loss.
With this epoxy resin kit, you will effortlessly create depth in your work. When you apply thin layers, you can rest assured that each layer will properly cure clear enough without becoming cloudy or discolored.
Dr Crafty Epoxy Resin - Best Clear Epoxy
Next up, we have this crystal clear epoxy resin from Dr Crafty. Ideal for resin molds, artworks, table tops, jewelry casting and other DIY projects around the home, this resin comes in 1 gallon or 2 gallon bottles, along with a pair of 16.9 oz measuring cups, two big sticks for mixing and a pair of plastic spreaders to help you apply the resin for a smooth and even finish. This resin is really easy to use, too; all you have to do is mix equal parts of resin and hardener at room temperature and you'll have 45 minutes to apply before it hardens.
TotalBoat Table Top Epoxy Resin - Another Top Pick
If you are looking for a super clear epoxy resin that offers a high gloss finish for bar tops, countertops, and tabletops, this resin will add tint and pigments to ensure your table looks unique and stands out in your home. In addition, you can also use this product as a craft resin to coat wooden gifts or casting jewelry and coasters. You’ll also find this epoxy is easy to use. All you need to do is mix 1 part resin and 1 part hardener, stir, then pour onto a surface - the epoxy levels without any assistance and will cure at room temperature. This product is also low odor, BPA-free, and does not have VOCs, so it is fantastic for indoor and shop use, provided you have suitable PPE and ventilation. Finally, each kit contains ½ gallon of resin and ½ hardener, so you should never run out of one or the other.
Loctite 1365736 Heavy Duty Epoxy - Runner Up
Loctite's heavy duty epoxy is almost as strong as the J-B Weld product, with 3500 PSI of tensile strength. Use it together with fiberglass cloth for even greater strength. This is a quick curing product, giving you a mere five minutes of working time. However, for many applications, that's enough. It works well with a wide range of substrates, regardless of whether they are porous or not. While waterproof, this epoxy product is not recommended for use in applications where it will be constantly submerged in water, nor should it be used in applications above 120 degrees Fahrenheit. It's amber clear in color, it can be tinted with earth pigments, cement, or sand, and once cured it can be sanded and drilled. This epoxy comes packaged in twin four ounce bottles.
Bob Smith Industries BSI-201 Quik-Cure Epoxy - Consider
This fast-curing epoxy from Bob Smith Industries cures to a slightly flexible consistency. This makes it perfect for use in applications where there is high vibration or substrates that are not totally rigid. This adhesive works with a wide range of substrates, including unusual ones like soft woods, hard plastics and white foam. Although it doesn't have the highest tensile strength, it cures quickly, giving you five minutes of working time and parts that are ready for handling in 15 minutes. It can be coated with polymer resin without affecting the curing of the resin, something that not all epoxies can do. Mixing it with microballoons (also available from Bob Smith) allows it to be used as a quick-setting putty, great for filling and repairing damaged wood. Packaged in two, four ounce bottles.
J-B Weld 8280 Original Steel Reinforced Epoxy - Consider
JB Weld is widely known as the champion in specialty epoxies for metal repair, especially on vehicles. This is the professional size of their steel-reinforced epoxy for metal repair. These larger 10 ounce tubes ensure you'll have plenty of epoxy on hand for many projects. I personally prefer buying my epoxy in larger packages like this, as it's both cheaper and I end up with less waste. Typically syringes and tubes always seem to go bad before I can use them all up. On the other hand, these larger bottles keep the two parts clean and separate, for easy use. This isn't a fast-drying epoxy, but rather one that gives you plenty of time for working with the metal. It sets in 4 to 6 hours and fully cures in 15 to 24 hours, depending on temperature. Once cured, this epoxy can be sanded and drilled. The tensile strength of this selection is 3960 PSI and can withstand temperatures up to 550 degrees Fahrenheit when fully cured.
System Three 0102K40 General Purpose Epoxy - Consider
T-88 is a true structural adhesive, which can be used for attaching wood parts together where fasteners might not be applicable, due to difficulty of installing the fasteners or expected problems with holding power. This epoxy cures to a transparent amber color that all but disappears when varnished. It is unique in that it can even be used on damp wood, without loss of strength. As long as the epoxy is worked into the wood with a brush. It's also incredibly strong, offering a tensile strength of 7,000 PSI when cured. It does not shrink when curing and remains flexible (even when fully cured) and will cure in temperatures as low as 35oF. The cured epoxy is unaffected by water, oil, kerosene and many other chemicals.
Marine-Tex Epoxy Putty - Best Wood Epoxy
This is a true marine epoxy, which can be used for bonding, filling, and repairing damaged wood. It works as well for fiberglass, making it ideal for bonding wood and fiberglass together. Featuring a creamy paste consistency, it can be applied on horizontal or vertical surfaces. The heavier body helps it to fill gaps and rebuild damaged components. For bridging holes, fiberglass cloth or any other sort of cloth can be used as a filler and strengthener. Finished repairs are fully waterproof, allowing this epoxy to be used below the waterline. Cured, this epoxy can be sanded, ground, drilled and tapped. It accepts paint and many other coatings well.
J-B Weld KwikWood Epoxy Putty - Best Wood Epoxy
In addition to the liquid epoxy that JB Weld makes for wood, they also provide an epoxy putty specifically formulated for working with wood. I believe this is the only epoxy putty specially formulated for wood that's available on the market. It is specifically formulated to use as a filler, repairing and rebuilding wood that has become damaged. It contains no solvents, so it will not stain, or leave any chemical residue which will soak through paints and other finishes. The epoxy putty has a 15 to 25 minute work life and fully cures in one hour. Cured, this epoxy putty provides 900 PSI of tensile strength. It can be machined (including drilling, tapping and sanding once it is cured) while the light tan color accepts paint well.
Permatex 84209 PermaPoxy 4 Minute Multi-Metal Epoxy - Best Metal Epoxy
The big issue with metal epoxies is the tensile strength of the cured adhesive and that's why I picked Permatex SteelWeld as the number one metal epoxy for this list. This product provides an amazing 4500 PSI of tensile strength once fully cured. This is actually a two-part epoxy, packaged in a twin-tube plunger which makes this product quite easy to work with as the plunger ensures equal parts of the epoxy are dispensed for mixing. It is a very fast-acting adhesive, giving you only four minutes of work time with a full cure taking hold in 24 hours. The cured adhesive can be drilled, sanded, or threaded in addition to also having excellent gap-filling capability.
JB Weld 8267 SteelStik Epoxy Putty Stick - Best Metal Epoxy
JB Weld SteelStick is a steel reinforced epoxy putty. That means it has steel flakes in it, as a filler. The steel flakes work like fiber reinforcement would, making the cured JB Weld a very hard mass. Once cured, JB Weld can be drilled filed and tapped, making it ideal for automotive or machinery repairs. It handles high temperatures well, up to 300 degrees, making it ideal for vehicle exhaust systems. The putty sets in five minutes and fully cures in 1 hour, resulting in a final strength of 900 PSI. Although it is steel reinforced, it won't rust.
Super Glue Plastic Fusion Epoxy Adhesive #15277 - Best Plastic Epoxy
Super Glue, the company who first gave us the adhesive by that name comes in as my number one choice for plastic epoxies. Their Plastic Fusion formula is an acrylic epoxy that not only works on plastic, but a host of other common materials as well. The twin-tube plunger gives you an equal amount of both resin and hardener which makes measuring and mixing easier. This adhesive gives you a three to five minute work time, with an 8 to 10 minute set time, taking on a light yellow color as well. That's a little longer than most fast-setting epoxies so you have plenty of time to position your parts and parts are cured enough for handling in 30 minutes. Capable of gap filling to 1/4", this epoxy has an amazing 4000 PSI shear strength, much more than the substrates that it will be applied on.
Loctite 1363118 Plastic Bonder Epoxy - Best Plastic Epoxy
Loctite's plastic epoxy is designed for use with a wide range of plastic substrates, including oily plastics, such as Nylon. It also works for: PVC, polycarbonate, acrylic, ABS, FRP, Mylar, Derlin, and phenolic as well. When you need to bond plastic to other materials, this epoxy works equally well with aluminum and stainless steel. Finished tensile strength is 3450 PSI and the twin plunger dispenser provides just the right amount of adhesive to mix for your project with full strength is reached in 20 to 25 minutes. This product is resistant to water, most common solvents, and shop fluids; however, it should not be used in applications where it will be completely immersed in water. It can be sanded and drilled when dry and the dry color of the epoxy is cream.
Permatex 84145 Permapoxy Black Plastic Welder Epoxy - Best Plastic Epoxy
Permatex bills their plastic epoxy as a "structural adhesive", a title which can actually be used with all epoxies. The difference here though is that they intend for their product to be used in structural applications, especially when plastics need to be bonded to other structural materials. This epoxy not only bonds to all common plastics hard and soft, but also to common architectural materials such as ceramics, wood, and composites. The mixed adhesives sets in 5 to 6 minutes and is fully cured to a "fixturing" point in 9 to 10 minutes. You can use this epoxy for gap filling up to 1/8" and it has good water resistance and chemical resistance. Cured strength is 3500 PSI and the color is black.
Rectorseal 97606 EP-400 Epoxy Putty - Best Putty Epoxy
Rectorseal is an industrial supply company, providing specialized products for the building and maintenance trades. They give us a little more to work with, by packaging their epoxy putting in a four ounce tube, rather than the conventional two ounces (they also have two ounces if you want). This is a fast-acting epoxy putty that fully hardens in 15 to 20 minutes, a third to a quarter of the time that its competitors do. You'll have to work quickly with it, but you won't have to wait a long time for it to cure. Once cured, it can be machined, sanded, painted and tapped. This epoxy putty can withstand temperatures up to 500 degrees and has been pressure tested to 1300 PSI.
POR- 15 49033 Epoxy Putty - Best Putty Epoxy
POR-15 provides products to the automotive repair market, including auto body repair. Their epoxy putty is intended for this market, to provide a means of filling damage, while bonding surfaces together. Unlike the other epoxy putties on our list, this one comes in two separate bars (rather than one with the two components side by side or concentric), so you have to cut them both off equally. That's actually an advantage, as it allows the unused putty to be stored longer. You can work it all the way up until the time it dries. Wetting your fingers allows you to smooth the surface, eliminating most sanding.
PC Products PC-11 Two-Part Marine Grade Epoxy - Best Waterproof Epoxy
This is a straight marine epoxy packaged conveniently in cans. While we're highlighting the one pound package here, it's also available in packages up to 10 gallons for those big projects. This pick has been special formulated for using underwater when necessary, so that repairs can be made underway. The high-tack mixture holds well to all surfaces, even vertical and overhead surfaces while working. If necessary, the epoxy can be reinforced with fiberglass cloth or wire screening, especially when working on large voids and gaps. This isn't a fast-drying epoxy, but rather one designed to give you ample working time for even the most difficult repairs. Once cured, the epoxy is an off-white color and can be sanded, painted, drilled, machined, cut or tapped.
J-B Weld 8272 Marine Weld Epoxy - Best Waterproof Epoxy
JB Weld's marine epoxy is specifically formulated for situations where metal parts need to be bonded together in a "cold weld" or to other surfaces and remain bonded even underwater. Although it is a marine epoxy and is waterproof once cured, it's not intended to be applied underwater. This is a high-strength epoxy, with a tensile strength of 3690 PSI. The epoxy sets to a grey color in four to six hours and is fully cured in 15 to 24 hours. Once cured, it can be shaped, filed, sanded, machined, drilled, and tapped. This selection comes packaged in separate tubes.
Pro Marine Supplies Table Top Epoxy Resin - Best Waterproof Epoxy
This is a different sort of marine epoxy, designed as a coating, rather than as an adhesive. Although it is a two-part epoxy product, it has a much thinner viscosity than most epoxies. It also cures to a high-gloss finish, making it an ideal coating for wood tables and trim on boats. Once cured it's waterproof, scratch resistant, and doesn't distort with age. Items coated are permanently preserved with a maintenance-free, high gloss finish. This is a two quart kit, but it's also available as a two gallon kit for larger jobs.
Buyer's Guide
The guide below contains the most commonly used types of epoxy, and a brief description of the intended use of each. This is by no means an exhaustive list and there are many specialty epoxies out there, so make sure to read each one and find the product that is right for you and the task at hand.
All-Purpose Epoxy
There are special purpose epoxy adhesives for all sorts of applications. But for most projects and repairs, a general purpose epoxy works just fine. Unless there's some reason to use a special purpose epoxy, you might as well use the all-purpose ones and save yourself the extra cost of those specialty adhesives.
In reality, the difference in an all-purpose epoxy and any specialty epoxy is minimal. That's not to say that there's no place for specialty epoxies, but in most applications the extra mile those adhesives go really isn't really necessary. Epoxy of any sort is one of the best, most powerful adhesives available so it's usually overkill for most projects. With that being the case, using a specialty epoxy can actually be nothing more than adding to the overkill.
The big advantage of sticking to an all-purpose epoxy is you only need to keep one product in your workshop, rather than a collection of them. That one product will do most of what you need, making it an ideal overall choice.
By minimizing the number of different adhesives that you stock, you justify going for larger containers of your all-purpose epoxy. That will save you a considerable amount of money, as well as reducing waste. I don't know about you, but I rarely make it through tubes of epoxy or the twin plunger pack, without the tubes getting plugged up, the cap getting stuck or the tubes breaking. When that happens, I end up throwing the rest away.
On the other hand, using larger containers (such as four or eight ounce bottles) is actually easier. Not only do you not run into shortages, but I have yet to have a problem with the package. So, even though it sits in my workshop longer, I get to use it all.
Like all epoxies, these are intended to be used in a 1:1 ratio, mixing equal parts of the two components. That makes it easy to get the right amount of material, each and every time. Always mix the two components thoroughly before application, so that they can begin to react and cure. If any part is unmixed, it will not cure and have to be cleaned up.
Wood Epoxy
Bonding wood can be a challenge, as compared to other substrates where epoxy might be used. The major issue with wood is that the substrate is often weaker than the adhesive being used to fasten it. This varies greatly, depending on the wood selected, as not all types of wood have the same structural strength.
Countering that is the fact that wood is a very easy substrate for adhesives to bond to. Although usually smaller than the human eye can see, wood is porous, allowing the epoxy to enter into the pores and get a good "grip" on it. This is magnified with open grain woods, like oak, which have more surface area for the epoxy to grip to. So, chances are that the epoxy isn't going to come loose of the wood. In fact, if the joint fails, it will be the wood itself that fails, not the adhesive to wood interface.
For this to work, it's usually best to use a low viscosity epoxy formulation, which will allow the epoxy to soak into the pores well. Coat surfaces well, before attaching, to ensure that the entire available surface area is used. Avoid using epoxy that has started to cure, as it won't soak into the wood pores and fiber.
While epoxy isn't used all that often with wood, there are some applications where it is an excellent combination. More than anything, we find it used in marine applications. Boats often have wood structures under their fiberglass skins. The two are often bonded together with epoxy, as using fasteners would cause the fastener heads to pull through the fiberglass.
In addition to using epoxy as an adhesive for wood, it can also be used as wood filler to combat damage, either due to accident, vibration or rot. In all cases, it is necessary to remove the damaged wood, so that the epoxy can make contact with structurally sound wood. While epoxy can help to stabilize damaged wood, it will not have any true structural strength. For that, it has to adhere to wood that has not been damaged.
When using epoxy to attach wood parts which are going to be finished, especially with stains and clear finishes like varnish, be sure to apply a coat of the finish to the wood, before using the adhesive. The epoxy's ability to soak into the pores of the wood will make it so that the finish cannot. This will cause places in the work which won't accept the wood stain, but look like they have been stained by some other type of finish.
Metal Epoxy
Perhaps one of the hardest materials to glue together is metals as there are two basic issues here. The first is having a surface that the adhesive can stick to, and the second is having an adhesive that's strong enough to provide a good metal-to-metal bond.
Bonding metals together with adhesives requires a different way of looking at the whole idea of joining metals. Typically, we join metals together with either fasteners or welding. In either case, only a small surface area is used for the bond. It's assumed that the strength of the metal itself will allow that small surface area to be sufficient, as the metal itself will spread the stress over a large area.
When using epoxy or other adhesives with metals, the joining area must be larger. You can't simply do an edge connection and expect it to hold, nor can you do a single spot by replacing a bolt or spot weld and then expect it to hold securely. The entire available surface area must be used in order to allow the greatest possible tensile strength for the adhesive. A large area of adhesives will obviously be considerably stronger than a small one, and will spread any forces to disassemble the joint across the entire area.
In this manner, two pieces of metal joined together by epoxy can be almost as strong as one piece. In restoration of vehicles, it's quite common for metal parts to be rusted thin to the point of not having enough structural strength. Bonding another layer of metal to the original part with the use of a good epoxy can provide as much strength as replacing the part itself. This type of repair is especially useful when the original part can't be removed for replacement.
The other issue which comes up, a surface that the glue can adhere to, requires a combination of two things. First of all, the surface needs to be clean of oils. Few adhesives will stick to oil and metal parts are often oily from their manufacturing and processing. The other thing that helps the bonding process is to rough the surface with a sander or grinder, giving the adhesive some "bite" into the metal. This rougher surface prevents the adhesive from peeling off by forcing it to conform to the surface.
Epoxies uses for metal must have some gap filling capability, as the metal parts often don't fit together perfectly; the adhesive must bond to both surfaces as well as fill the space between them. Epoxies are excellent for this as they are heavy-bodied. Some of these have metal filler in the epoxy as well which further improves their gap filling capability.
Epoxies for metals can be both two-part liquid and epoxy putties. Where there's a need to replace missing material, epoxy putty is a better choice. In cases where the metal parts fit tightly together, use of a two-part liquid is better.
Once cured, these epoxies are often drillable and even threadable for fasteners. This must be done with care, as the epoxy is not as strong as the original metal. However, threaded fasteners can be used, especially when the fastener is also holding to the metal parts.
Plastic Epoxy
Plastics can be difficult to bond together due to their variety in hardness, texture and natural oiliness. But getting the plastics to bond isn't the whole battle. Once bonded, many plastics will fail either at the bond itself or at the edge of the adhesive. A flexible adhesive is needed to prevent adding stress to the parts which will ensure they'll likely break again.
While there are some adhesives designed specifically for plastics, they're usually designed with one specific type of plastic in mind. In most cases, these adhesives work well with that particular plastic and under specific parameters. However, they're rarely able to handle high stresses.
On the other hand, epoxy is a very strong adhesive with a high tensile strength which makes it excellent for pretty much all types of plastics. As a two-part adhesive it's not affected by the plastic itself, being totally self-contained as far as curing is concerned. Cured epoxy will often actually make a plastic part stronger than it was before.
You can even use epoxy for edge gluing of plastics, one of the hardest bonds to accomplish, due to the small surface area. Typically, edge glued plastics separate easily as soon as any lateral pressure or bending is applied. This is much less likely to happen with use of an epoxy product.
For additional strength, epoxy can be used in conjunction with fiberglass cloth. This is exceptionally good when high strength is needed for parts that are edge glued together (such as a fitting being glued to a tank) without an adequate flange. Sections of plastic pipe can be connected together in this way or repairs can be made to recreational vehicle waste storage tanks. The epoxy is more flexible than fiberglass so it isn't brittle, even with the fiberglass cloth reinforcement.
Some plastics, such as polyethylene, polypropylene, and Teflon, are designed to provide non-stick surfaces. No adhesives should be used with these types of plastics and that includes epoxy.
Typically, a fast cure time is desirable when working with plastics as it's hard to hold the parts together or clamp them firmly. It's important to clean the surfaces before bonding them, especially when working with oily plastics like nylon. However, any molded plastics can be oily due to the mold release compounds used in their manufacture.
Putty Epoxy
Epoxies are great for many situations, but they are not gap filling. While additives can be put in the epoxy to make it gap filling, few gap filling epoxies are available on the market. For small jobs, most people turn to epoxy putty.
Epoxy putty is a two-part plastic adhesive, made of the same basic chemicals as epoxy. The main difference is that the putty is solid, rather than liquid like other epoxies. This makes it possible to be used for gap filling needs, as well as places where structural strength needs to be added. When epoxy putty is wrapped around a joint and allowed to harden, it strengthens that joint, much like putting a cast on a broken bone.
Once cured, epoxy putties are at least somewhat machinable, meaning that it can be drilled, sanded, ground and even tapped to put screws into. Some manufacturers claim that their epoxy putties are as strong as steel. This is true, but only as measured by shore rating (hardness), not tensile or sheer strength.
The biggest problem with using epoxy putty is that of adhesion. All adhesives gain most of their adhesion from filling in the grain in the substrate material and then bonding to it. The irregularities in the surface provide shear strength to the bond. Since epoxy putty is in a putty form, it doesn't flow into the materials natural grain, adhering to it. Rather, it is necessary to push the epoxy putty into the grain, so that it can grab.
The other problem is that of ensuring a clean surface for the putty to adhere to. Liquid epoxies may displace grease or dirt on the substrate surface, or even mix them, but epoxy putty won't. It needs a clean surface, free of grease dirt or other solvents. Failure to provide a clean surface is the most common cause of failure when working with epoxy putty.
Epoxy putty is commonly sold in sticks of about two ounces, but is also available in larger quantities for industrial or commercial purposes. If you use a fair amount of it, it is ultimately cheaper to buy it in these larger quantities.
Waterproof Epoxy
While epoxies are some of the strongest adhesives in the world, they aren't perfect and have their weaknesses. One of those weaknesses is dealing with water. While water won't fully dissolve epoxy, it does affect an epoxies structure and ultimately weakens it. This makes it so that epoxies are not waterproof, but merely water resistant. Therefore, there's a need to add a stabilizer to the epoxy when used in applications where the epoxy is likely to be submerged in water.
These additives are normally added to the epoxy at the factory, rather than in the field. However, it's possible to buy them and add them yourself if you like the extra work the process entails. Usually the easiest way to make sure epoxy has waterproof capabilities is to buy ones that already have the additive in them.
Generally speaking, these waterproof epoxies are referred to as "marine epoxies" because they are primarily used for the manufacture and maintenance of boats. All marine epoxies are water stabilized, ensuring that their bond isn't compromised by continual submersion in water.
One nice thing about marine epoxies is they come in a wide variety of forms. Rather than just liquid and putty, we can also find gel and paste epoxies which provide greater gap filing capabilities than liquid epoxies while being easier to form than putty epoxies. There are also low viscous epoxies which can be used as a protective coating for teak or other woods used in marine applications.
Like all other epoxies, these are two-part adhesives which must be mixed to cure. Curing is a chemical reaction rather than the drying most adhesives depend upon. This means that these adhesives will cure in any environment, even when they're submerged in water.
Marine epoxies are often high gloss so they can be used without having to finish them. However, like other epoxies they can be sanded, drilled and cut, once they've set. This allows forming the final part (including the epoxy) as if it were one solid piece. When painting glossy-finished epoxies it's a good idea to sand the epoxy before applying the paint so as to ensure good adhesion by the paint.
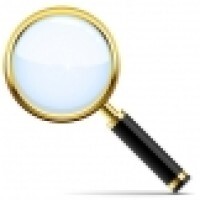